Laminate
Today laminated floors are widely used in studies, boutiques, railway stations, restaurants and surely in residential buildings. An advantage of laminate is its cost. It is substantially lower than the cost of parquet or solid board while they look almost alike. Laminate color and texture may vary greatly.
Laminate performance exceeds even that of natural wood.
Main laminate advantages
low flammability (reduces the risk of fire)
High mechanical stability
Low toxic level (made of natural stock)
Retaining appearance even at heavy loads
Safe for allergic individuals as almost does not contain junctional spaces where dust can accumulate
Easy treatment
For laminate to serve a long life it shall be selected in accordance with its application conditions.
Every laminate consist of at least 4 layers:
1. Protective layer (protects laminate plank and decorative layer).
2. Decorative ornament.
3. Plate (base).
4. Stabilizing layer (for perfect junction of laminate with the floor)
All the types of laminated floors are divided according to the classes of wear resistance. These classes are the basic indexes of floor life.
Laminate floor load classes:
31st class – small load degree: hotel room, apartment
32nd class – medium load degree: offices, shops, restaurants
33rd class – high load degree: warehouse, railway station.
Laminate laying
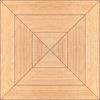
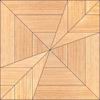
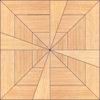
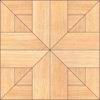
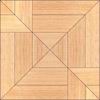
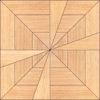
There exist two types of laminate laying technology: adhesive and glueless (interlocking). Planks of glue laminate are butt-joined and glued by tongue-and-groove. While mounting the glue covers coupled plank elements forming firm solid covering. This laying method provides good water proofing of the floor. Planks of glueless laminates are interlocked. The main advantage of interlocking method is simple and fast laying and possibility to change a plank if damaged.
Laminated planks laying is performed without adhesion or fastening to flooring underlayment, only plank ends are joined. Therefore, laminate is a “floating floor”. Tongue and groove are connected by means of special glues or by glueless method depending on the laminate type. For plank joints to be less discernable planks are recommended to be laid in the daylight direction. Spaces of not less than 10 mm shall be left along all the walls. The first row of planks is laid so the grooves face the wall, the last plank shall be cut leaving a space near the wall. The length of section cut shall not be less than 30 cm. The second row starts with cut section of the first row panel. When glueing planks the glue is put on all the surface of groove end. After junction of elements excessive glue is removed with wet sponge and the place of joint is to be rub dry. When the last section of each raw and all the sections of the last row are laid foot bearing should be used. After laminate has been laid one should not walk on it at least 24 hours – until the glue dries completely. Laminate floor can be finished with boarders fixed to walls.
Laminated planks laying is performed without adhesion or fastening to flooring underlayment, only plank ends are joined. Therefore, laminate is a “floating floor”. Tongue and groove are connected by means of special glues or by glueless method depending on the laminate type. For plank joints to be less discernable planks are recommended to be laid in the daylight direction. Spaces of not less than 10 mm shall be left along all the walls. The first row of planks is laid so the grooves face the wall, the last plank shall be cut leaving a space near the wall. The length of section cut shall not be less than 30 cm. The second row starts with cut section of the first row panel. When glueing planks the glue is put on all the surface of groove end. After junction of elements excessive glue is removed with wet sponge and the place of joint is to be rub dry. When the last section of each raw and all the sections of the last row are laid foot bearing should be used. After laminate has been laid one should not walk on it at least 24 hours – until the glue dries completely. Laminate floor can be finished with boarders fixed to walls.
Parquet Polishing
No matter how carefully parquet is laid, it is almost impossible to obtain the perfect surface. Therefore, to even the parquet ultimately and to reach the characteristics required a complex of work is to be implemented. Depending on the parquet state and customer’s wishes the following technological operations can be performed:
SCRAPING
Preparatory polishing (scraping) is made using a belt sander to remove old lacquer, mud, minor defects, scratches and wood warping.
POLISHING
Polishing – final evening of the surface and removing of scratching signs – crimp, shagreen and grain raising. Parquet floor polishing is performed in several steps using grinding equipment with dust collectors. With every next step the size of abrasive grit is reduced. The number of polishings depends instantly on the quality of underlayment (screed) prepared and veneer laid.
SPACKLING
Spackling – filling cracks between parquet blocks or modules with special pastes. It is usually performed after scraping.
PRIME COATING
Prime coating – putting primers impregnating surface wood layer to protect it from the exposure of chemical substances and mechanical loading and to eliminate the adhesion of parquet block edges. Prime coating prepares parquet surface for lacquering.
LACQUERING
Lacquering, oiling and waxing are performed for the surface to acquire required esthetic qualities and to increase wear-resisting properties of the parquet floor. The number of coatings is defined by physical and chemical properties of the substance.
FILLING PORES
Filling pores – filling wood pores with special compositions (gels) to prevent caving in of lacquer coating and for parquet floor to look filled.
INTERLAYER POLISHING
Interlayer polishing removes grain raising while lacquering.
Basic requirements set to the premises where parquet works are performed:
Completion of all damp, finishing and dust works (tile paving, walls and ceiling finishing, etc.) in all the premises where parquet is laid and adjacent ones.
No garbage and foreign objects in the premise.
No garbage and foreign objects in the premise.
Adhering to temperature-humidity conditions (air temperature should range between 20 and 24 C, relative humidity should range between 45% and 60%).
Possibility to connect equipment to a power circuit.
After parquet works have been finished one may perform wallpaper hanging, painting of walls, door and door frame assembling.
Possibility to connect equipment to a power circuit.
After parquet works have been finished one may perform wallpaper hanging, painting of walls, door and door frame assembling.
Parquet Scraping
Scraping is an obsolete technology of surface evening by means of a cutting tool: hand scraper or grinding machine with knife drums. The best modern method of surface evening is parquet polishing with abrasives. Therefore, parquet scraping shall mean parquet polishing. German belt sanders and flat polishers are used. First rough grinding evens the floor (abrasive grit of 40-60 removes unevenness), and then the evidence of rough grinding is removed by consecutive grit change: 80, 100, 120. Interlayer varnish coats are polished by flat polishers with low abrasive grit or special net.
Our company performs high quality parquet scraping along with spackling, varnishing and polishing. We have unique foreign equipment for evening, scraping and polishing of large surfaces. We perform parquet scraping without dust and mud.
We guarantee the quality of our parquet works. Our workers are real experts. Scraping can be performed at any time convenient to you.
Finishing
Prime coating of polished parquet surface shall impregnate all wood pores with special composition, reduce varnish consumption during subsequent coating, protect wood surface against direct influence of varnish components and preserve natural wood color as far as possible. Prime coating mixtures are usually put using pullets, equalized by polishing nets and then covered with 1-2 coats of priming varnish. Sometimes for better revealing of wood texture and giving it the necessary color (walnut, cherry, mahogany, etc.) polished parquet is coated with special mordants or coloring agents.
The same effect can be reached by tinting varnishes. Multiple varnish coatings of the surface protect floor from moisture and mechanical rubbing loads, produce optical effects when some elements of floor image acquire contrast color or seem volumetric. Depending on the quality requirements, 3-7 coats of varnish are put with intermediate interlayer polishing. It is very important to observe the time of every coat drying recommended by manufacturer. The quality of varnish surface depends much on the dustiness of the premise. Therefore, frequent vacuum cleaning and wet cleaning shall be performed. In some cases it is necessary to isolate the surface of walls and ceiling with polyethylene film. While varnishing draughts are unacceptable and all the equipment that creates air flow or turbulent flows shall be turned off. All the polishers shall necessary have built-in dust collectors.
The same effect can be reached by tinting varnishes. Multiple varnish coatings of the surface protect floor from moisture and mechanical rubbing loads, produce optical effects when some elements of floor image acquire contrast color or seem volumetric. Depending on the quality requirements, 3-7 coats of varnish are put with intermediate interlayer polishing. It is very important to observe the time of every coat drying recommended by manufacturer. The quality of varnish surface depends much on the dustiness of the premise. Therefore, frequent vacuum cleaning and wet cleaning shall be performed. In some cases it is necessary to isolate the surface of walls and ceiling with polyethylene film. While varnishing draughts are unacceptable and all the equipment that creates air flow or turbulent flows shall be turned off. All the polishers shall necessary have built-in dust collectors.
Gloss, semimatt and matt varnishes are used according to design or customer wishes. The floor can be entirely covered with single varnish type, or varnishes with different surface types can be used depending on the functional purpose of separate premises (bedroom, study, children’s room). Likewise clear and tinting varnishes can be used. Varnishes used in parquet works differ by their composition and base, they include polyurethane, acrylic and water-based, single and manycomponent varnishes and those with hardeners. It is important to use proved varnishes of well-known producers that include a number of Scandinavian, German, and American companies.
Wax and special oils for parquet surface protection are used less frequently. Nevertheless, these waxes and oils that make parquet treatment somewhat more complicated in the process of exploitation (using electric floor polishers once a week) make parquet floor virtually ageless if regular varnish change (every 4-5 years) is excluded.
Wax and special oils for parquet surface protection are used less frequently. Nevertheless, these waxes and oils that make parquet treatment somewhat more complicated in the process of exploitation (using electric floor polishers once a week) make parquet floor virtually ageless if regular varnish change (every 4-5 years) is excluded.